Material Transport
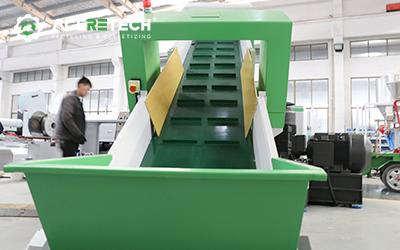
Feeding
As standard design, plastic scraps such as film, filament, raffias conveyed into the compacting room through belt conveyor; to handle rolls’ scraps, roll hauling off device is an optional feeding method. Motor drives of conveyor belt and hauling device cooperate with ABB inverter. Feeding speed of conveyor belt or roll hauling off is fully automatic based on how full the compactor’s room is.
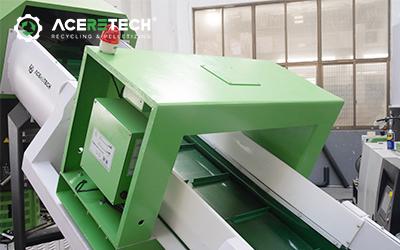
Metal Detectors
Metal detector can be combined with belt conveyor, and can interlock with control system, to warn and stop the system, in case that metal is found in feeding.
Crushing and Compacting
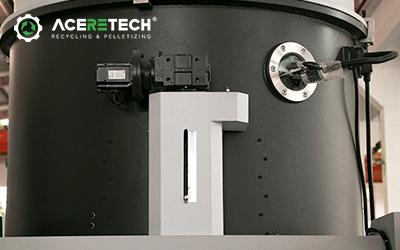
Sliding Gate With Servo Motor
It can handle both hard and soft materials. The sliding gate controls the residence time of the material in the compactor to achieve the effect of pre-drying and ensure that clean and dry material enters the barrel. Material that fails to achieve the treatment effect will not be able to enter the next process. PLC accurately controls the quantity of forced feeding materials to ensure production capacity.
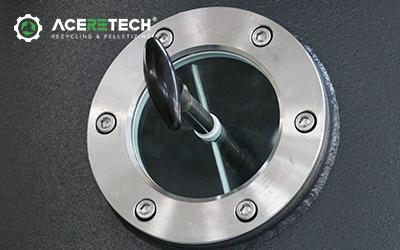
High-brightness Lamp Tube
Equipped with a high-brightness lamp tube, it is designed for viewing the material situation in the compaction chamber. The lamp tube uses high-quality LED lamp beads, with uniform light and sufficient brightness. The operator can intuitively observe the distribution of materials in the compaction chamber and adjust the feeding speed and compaction degree in time to ensure the smooth progress of the granulation process. In addition, the shell of the lamp tube is made of materials with a high protection level, which effectively prevents dust and moisture from invading, ensuring the long-term stable operation of the lamp tube.
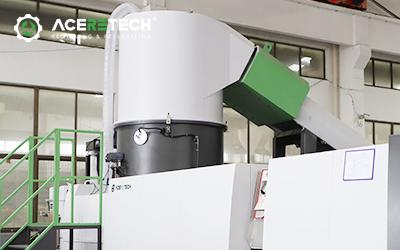
Compacting
Rotary blades on the knife-disk and fixed blades on the wall cut plastic material into small flakes. Heat which caused by high speed friction pre-heats and dries the flakes and make them shrink.
Arc-shaped plates guide the material down and into the extruder under the centrifugal force of knife disk.
This combined process of size-reduction, pre-heating and compacting enables stable and effective feeding for small bulk density plastics.
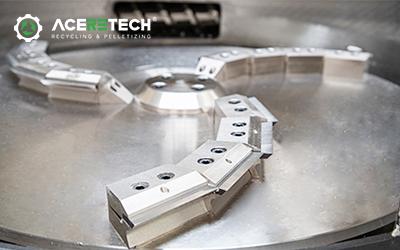
The Rotatory Blades of Compactor
The rotating blade and fixed blade cut the material into small flakes. The friction heating generated by the high-speed rotating blades will per-heat and shrink the flakes.
Intelligent Control

Remote Monitoring and Information Transmission
System program remote monitoring and transmission system,bluetooth both are available for ACS plastic pelletizing line realizing functions of remote monitoring and information transmission.
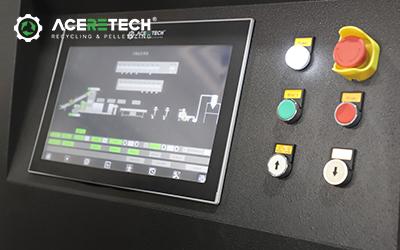
Intelligent Control
Intelligence Start: One button only Following set logistical sequence and materials processing requirement, interlocked system modules can start by "one button only” Intelligence Stop: One button only Each related modular part in ACS system available to shut down by only one button. Emergency Stop Emergency stop function is available in ACS plastic pelletizing system in case that uncertain risk occurred during machine running.
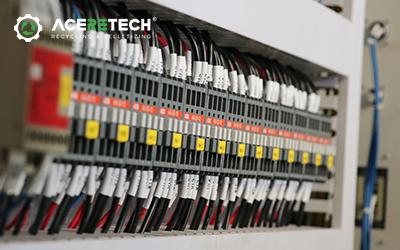
European Appliances
The electrical equipment uses selected European brand electrical components to ensure the efficiency and safety of the equipment during operation.
The equipment power distribution system is reasonably designed, with clear line layout, which effectively reduces the failure rate.
Single Screw Extruder

Barrel
Because of the super L/D ratio, the single stage extruder in the production line can be used as a double- stage extruder. After the middle double-piston type screen filter, another filter can be added at the end. The double filter standard can improve the quality and performance of the final product particles.
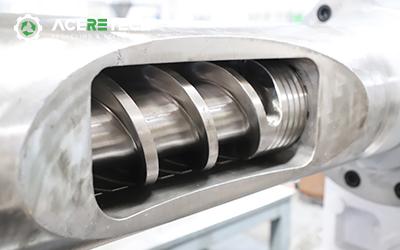
Single Screw Extruder
Our unique design single screw extruder gently plasticizes and homogenizes the materials. Our bi-metal extruder has great anti-corrosion resistant, wear resistant and long life time.
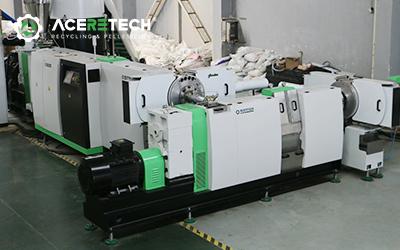
Two Sets of Single-Screw Extruders
It consists of two sets of Single-Screw extruders , suitable for printing ink heavy, high moisture content, poor fluidity and temperature sensitive, high impurity content materials which requires the double filtration system, multiple exhaust and other higher requirements, and a longer process.
Double Vacuum Degassing Zones
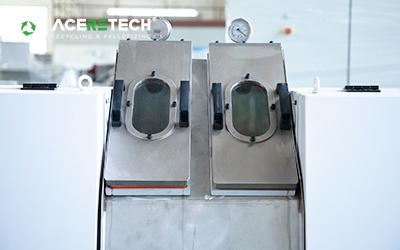
Double Vacuum Degassing Zones
With double vacuum degassing zones, volatile such as micro-molecules and moisture will be removed efficiency to improve the quality of granules, especially suitable for the heavy printed materials.
Filtration System
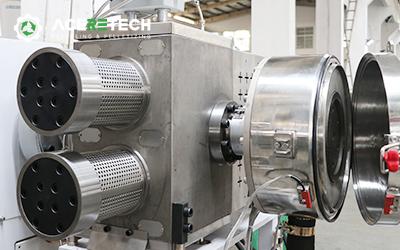
- A regular single-plate/piston double-station screen changer or non-stop double plate/piston four-station can be installed on head of extruder to present significant filtration performance.
- Long screen lifetime, lower screen change frequency: Long filter lifetime owing to large filter areas.
- Easy to use and none-stop type: easy and quick screen change and do not need to stop the running machine.
- Very low operation cost.
None-Stop Piston Type Filter
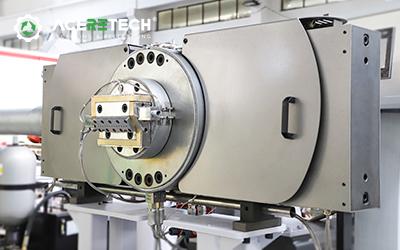
Plate Type Filter
The Plate type filter is made in a continuous type with two filter plates. There is at least one filter working when the screen is changing.Ring-shaped heater for consistent and stable heating.
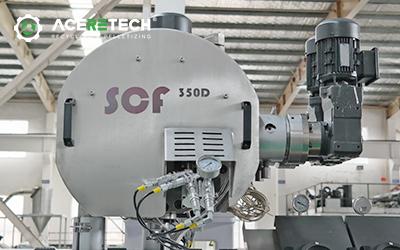
Self Clean Filter
This model combines our self-developed self-cleaning filter.The new SCF self-cleaning filtration system makes non-stopping recycling extrusion, especially suitable to highly contaminated materials re-pelletizing. SCF filtration system can handle and remove up to 5% contaminates in the melt flowing, can separate the contaminates as: paper, wood, aluminum, unmelted plastic and rubbers etc.
Pelletizing System
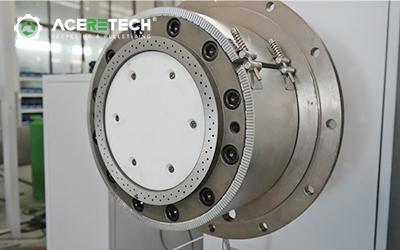
Die Head
This is the most appropriate process for the need for better melt filtration and higher production. In the first stage,two or more single screw extruders can be designed for the two-stage pelletizing production line, and then they can enter the second-stage extruder at the same time.
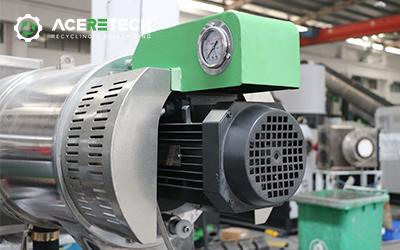
Water Ring Pelletizing System
- Self-adjusting pelletizing head for the best granulate quality and long uptime thanks to consistently correct blades pressure.
- RPM of rotatory blades is automatic based on melt extruding pressure.
- Easy and fast pelletizer blades changeover, without adjustment work saves time
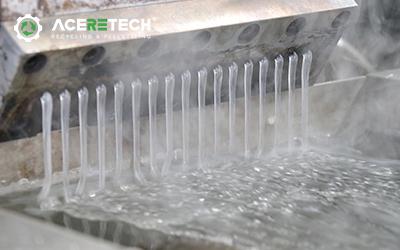
Strand Pelletizing
The strip-shaped Melted plastic strands passes through the cooling water tank and is quickly cooled and solidified. During the cooling process, the strip is pulled out by the traction device, maintaining a certain speed and stability. Then, the strip enters the pelletizer and is cut into pellets of a certain length by the rotating cutter.
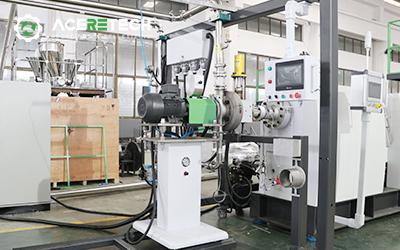
Under-Water Pelletizing System
Highly automatic pelletizing system. It is suitable for materials with high MFI and high production capacity requirements. This system includes pelletizer, valve, conveying pipeline, dewatering vibrating screen, silo.
Vibration Dry
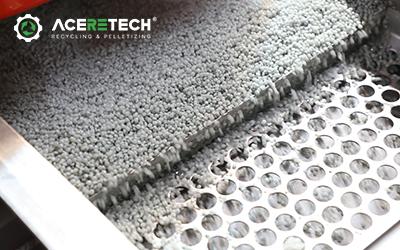
Vibration Dry
- Advanced dewatering vibration sieve combing with horizontal-type centrifugal dewatering present high performance dried pellets and lower energy consumption.
- Assemble sieves: The sieves are installed and fixed by screws instead of welding, so you can change the sieves easily in the future.
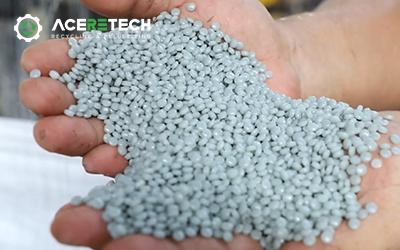
Plastic Particles
Final output: plastic particles,the plastic pellets can be re-used for producing high quality plastic products once again.
Packing System
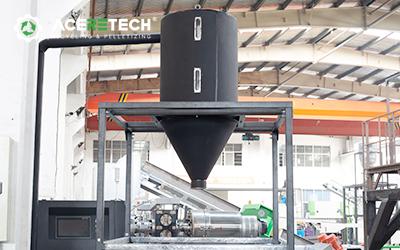
Packing System
- Final qualified granules store here,the drying shaker together with the horizontal centrifuge can get a good drying result, and less energy consumption.
- Capacity online monitoring & Quantitative weighting system.