Chain Plate Conveyor
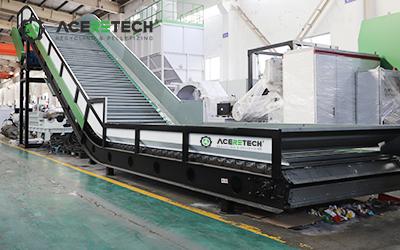
The PET plastic bottle washing line is equipped with chain plate conveyor, which is wide and convenient for the transportation of plastic waste bottles
De-Baler
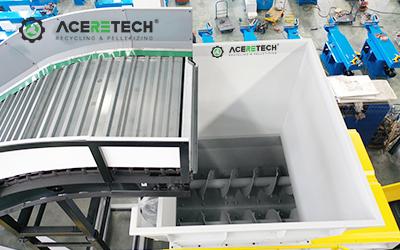
De-baler is mainly used to break up compacted waste plastic bottles, so that they can be loosened and better entered into the next process.
Belt Conveyor

Conveying raw materials into next parts. Controlled by inverter, belt speed is adjustable.
Function: bottles conveying
Width of belt: 1000mm
Basic material of belt: PVC
Motor power: 2.2KW
Trommel
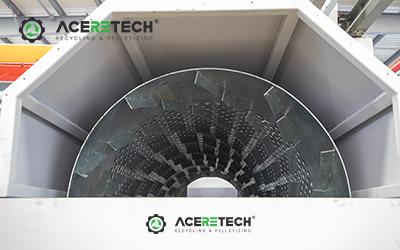
Function: remove stone, dust, loosen caps and small metal
Basis material: Galvanized carbon steel
Frame: Carbon steel
Diameter of barrel : 1500mm
Length : 5000mm
Motor power: 5.5KW
The hole diameter:50mm
Ferrous Remover
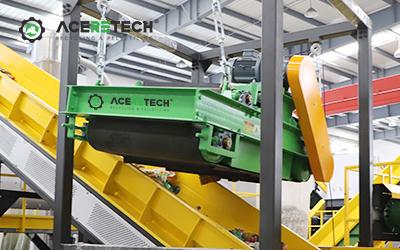
Function: Equipped above the conveyor belt, used to remove iron, chromium, manganese and other ferrous
Power:3KW
Label Remover
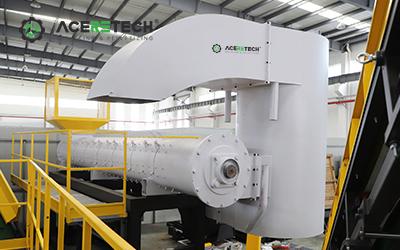
Function: remove above 90% labels for both common and compressed bottle
No flakes waste and no water consumption
Motor power: 15KW
Suction fan power: 5.5KW
Rotary blade : 42pcs ( teeth 378pcs )
Fixed blade : 45sets * 4 = 180pcs ( teeth 1080pcs )
Pre-Washer
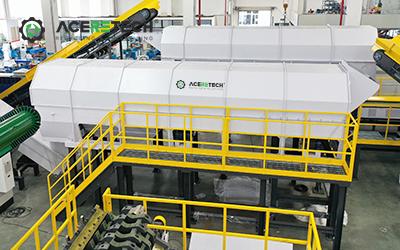
Function: bottle washing, remove small size impurity, decrease the working pressure for down stream. Tank body SS304
Diameter:1500mm
Length:6000mm
Motor power:7.5KW
Power of screw:2.2KW
Diameter : 250mm
Disk Separator
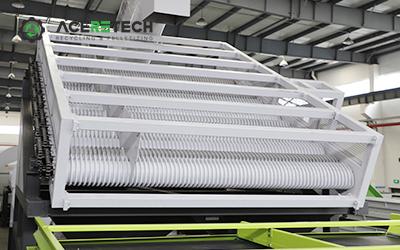
Equipped with multiple rolling screws, the material is screened by rolling, and the impurities can fall from the gap to the impurity receiving port below.
Bouncing Screen
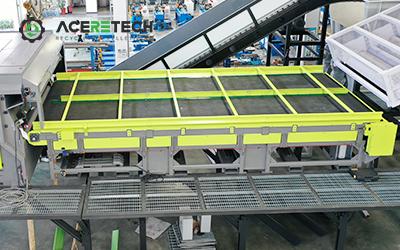
Equipped with a disk separator, PET plastic bottles pass through the bouncing screen to remove loose impurities, labels, caps, etc.
Bottle Sorting Machine
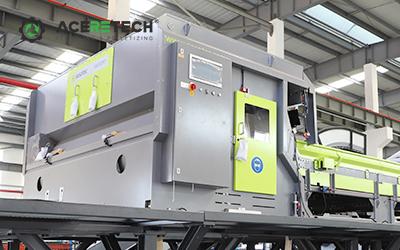
The material sorting of the whole bottle can be sorted according to factors such as the color required by the customer, and the PET bottle of the same color category can be carried out to the next process.
Manual Sorting
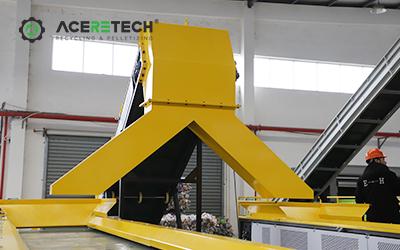
The material is divided into two double stations through manual sorting for manual sorting
Crusher
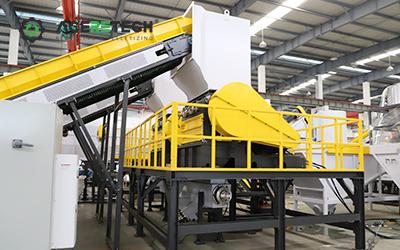
Divide large-size raw materials into relatively uniform small-size raw materials through crushing.
Crushing bottle to small flakes.
Disk Separator
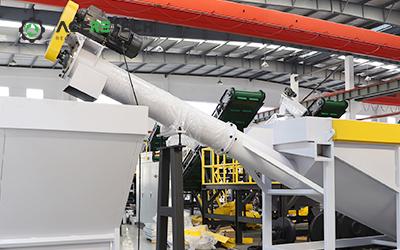
Function: PET flakes conveying
Motor power: 4KW
Dia. of screw: 310mm
Part contact with raw materials: stainless steel
Separation Floating Tank
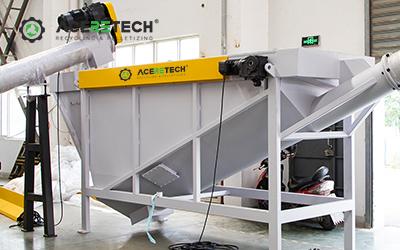
Function: wash flakes and remove floating material as PP,PE and Caustic Soda
Motor power of screw loader: 5.5KW
Motor power of thumbwheel: 0.55KW
Quantity of thumbwheel: 3 sets
Dia. of screw:250mm
Part contact with raw materials: stainless steel<
Equipped with water tank and pump
Label Separator
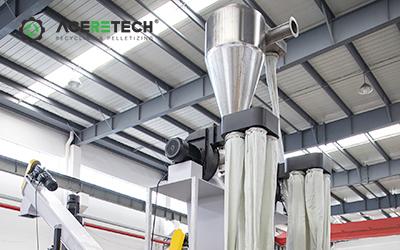
Remove impurities such as residual PET bottle labels
Hot Washer
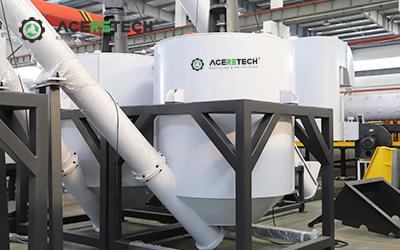
Function: after hot washing, it’s easier to remove oil, glue
Motor power: 5.5KW
Volume of hot chamber≈4.07 m3
Outer layer: Carbon steel
Inner layer: stainless steel
Middle layer: rock wool for insulation
Caustic soda percentage:1-2%
Temperature of hot water:70-90 centigrade
Non-stop flakes feeding and loading out
High Speed Friction Washer
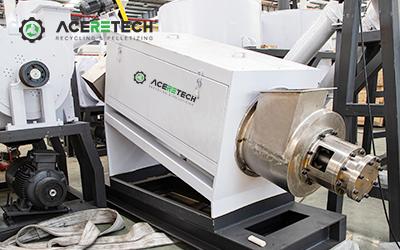
Function: remove the glue and dirty
Motor power: 30KW
Motor power of water pump:1.5KW
Rotary speed of screw: 1200rpm
Part contact with raw materials: stainless steel
Centrifugal Dryer

Function: Drying and flakes moisture reach 2%
Motor power: 22KW
Motor of cover open:0.75KW
Rotary speed of screw: 2200rpm
Part contact with raw materials: stainless steel
Pipeline Dryer
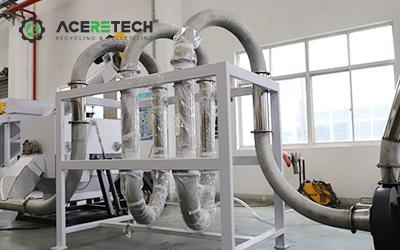
Function: hot air drying, moisture < 1%
Heating power: 48KW,if adopt steam heating, this electric consumption will be saved
Power of blowing motor:5.5KW
Power of suction motor: 5.5KW
Vibration Dryer
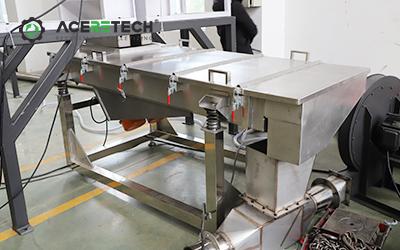
Drying of washed PET bottle flakes through a vibrating sieve
Intelligent Control System
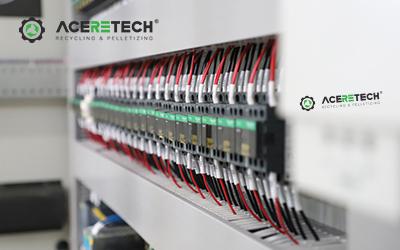
With CE/CSA/TUV/SGS/ISO standard, all parameters can be set on the touch screen.
1.Electric control component: (Schneider), e.g. Circuit-breaker, AC contact, press button, pilot lamp.
2.For electrical controlling of the entire system.
3.Safety interlock principle.
4.All electrical units: LS, Schneider, ABB.