Material transport
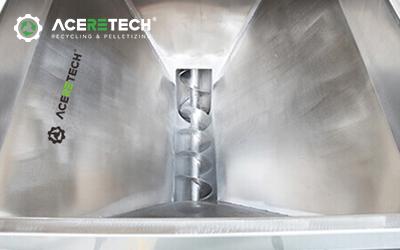
Screw Loader
Lumps or thick flakes after crushed, conveyed into the single screw extruder by screw loader, then, compress, plasticize in the extruder and removed volatiles and moisture by vacuum system, after filtering through the filtration system, to pelletize into granules. Depending on the different screw diameters of single screw, the typical capacity can cover from 100kg/h to 1000kg/h,Loading motor power: 2.2 kw. Conveying pipe made with stainless steel material, pipe inner thickness is 2mm, pipe diameter is 102mm.
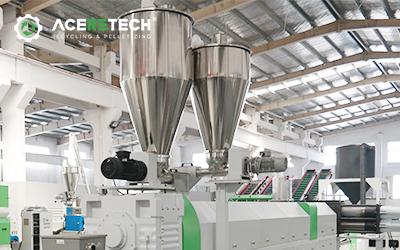
Main feeder (Volumetric)
Metal detector can be combined with belt conveyor, and can interlock with contrl system, to warn and stop the system, in case that metal is found in feeding.
Gear Box
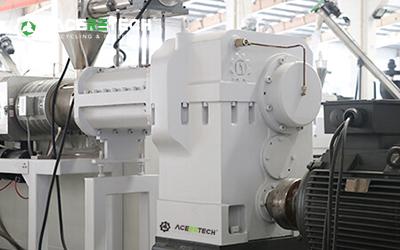
Gear Box
The gearbox will reduce the motor speed to the screw shafts speed and distributes it to the two output shafts.Low-noise, high torque output.
Double Screw Extruder
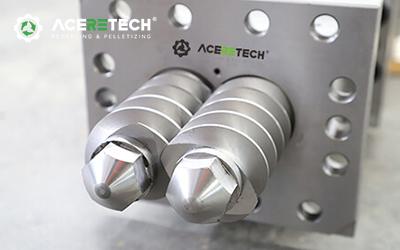
ATE Parallel Twin Screw Extruder
The twin screw extruder will gently plasticizes the materials.our unique bi-metal twin screw extruder has greater homogenization efficiency and long life time.
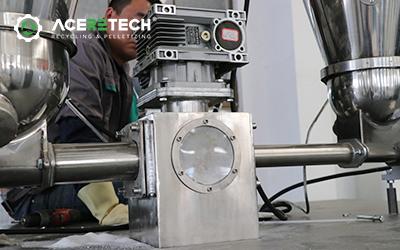
Silo Light Tube
Can watch the working state of the machine.
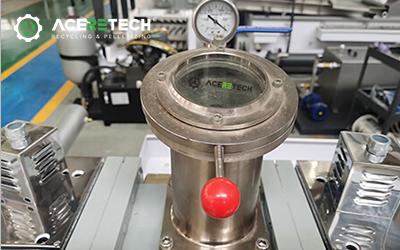
Vacuum Degassing System
This vacuum system will remove the volatile in the agglomerates and improve the quality of granules. It equipped one-channel value to avoid water back-flowing.

Cast Copper and Aluminum Heater
Cast copper and aluminum heater , easy to assemble and disaassemble. Faster heating and low energy waste.
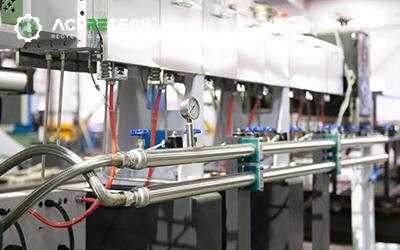
Soft Water Cooling System
Material of input and output pipes is stainless steel. Manual valves to adjust flowing rate of cooling water; solenoid valves are to control opening and closing of cooling water flowing in.
Filtration system
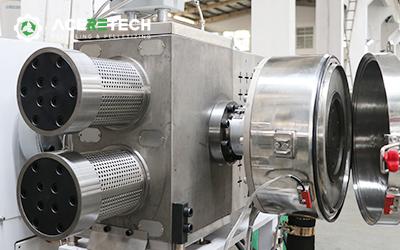
- A regular single-plate/piston double-station screen changer or non-stop double plate/piston four-station can be installed on head of extruder to present significant filtration performance.
- Long screen lifetime, lower screen change frequency: Long filter lifetime owing to large filter areas.
- Easy to use and none-stop type: easy and quick screen change and do not need to stop the running machine.
- Very low operation cost.
None-Stop Piston Type Filter
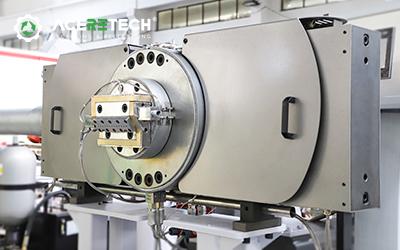
Plate Type Filter
The Plate type filter is made in a continuous type with two filter plates. There is at least one filter working when the screen is changing.Ring-shaped heater for consistent and stable heating.
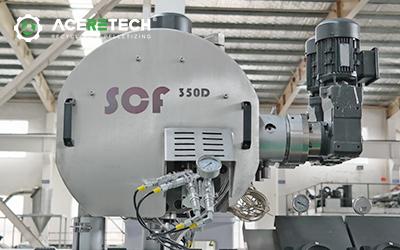
Self Clean Filter
This model combines our self-developed self-cleaning filter.The new SCF self-cleaning filtration system makes non-stopping recycling extrusion, especially suitable to highly contaminated materials re-pelletizing. SCF filtration system can handle and remove up to 5% contaminates in the melt flowing, can separate the contaminates as: paper, wood, aluminum, unmelted plastic and rubbers etc.
Pelletizing system
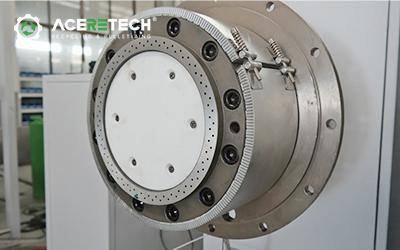
Die Head
This is the most appropriate process for the need for better melt filtration and higher production. In the first stage,two or more single screw extruders can be designed for the two-stage pelletizing production line, and then they can enter the second-stage extruder at the same time.
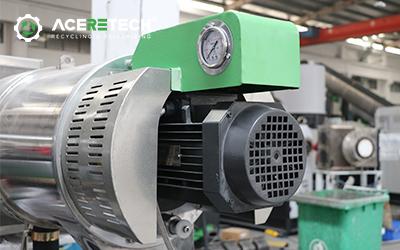
Water Ring Pelletizing System
- Self-adjusting pelletizing head for the best granulate quality and long uptime thanks to consistently correct blades pressure.
- RPM of rotatory blades is automatic based on melt extruding pressure.
- Easy and fast pelletizer blades changeover, without adjustment work saves time

Strand Pelletizing
The strip-shaped Melted plastic strands passes through the cooling water tank and is quickly cooled and solidified. During the cooling process, the strip is pulled out by the traction device, maintaining a certain speed and stability. Then, the strip enters the pelletizer and is cut into pellets of a certain length by the rotating cutter.
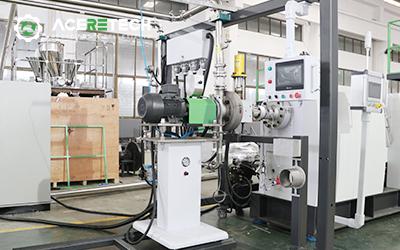
Under-Water Pelletizing System
Highly automatic pelletizing system. It is suitable for materials with high MFI and high production capacity requirements. This system includes pelletizer, valve, conveying pipeline, dewatering vibrating screen, silo.
Vibration Dry
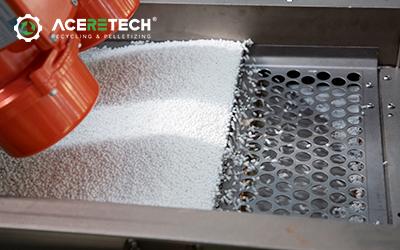
Vibration Dry
- Advanced dewatering vibration sieve combing with horizontal-type centrifugal dewatering present high performance dried pellets and lower energy consumption.
- Assemble sieves: The sieves are installed and fixed by screws instead of welding, so you can change the sieves easily in the future.
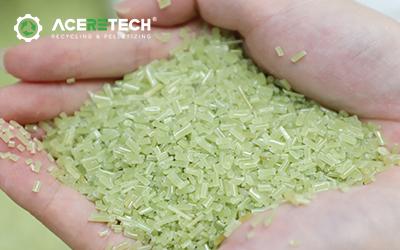
Plastic Particles
Final output: plastic particles,the plastic pellets can be re-used for producing high quality plastic products once again.
Packing System
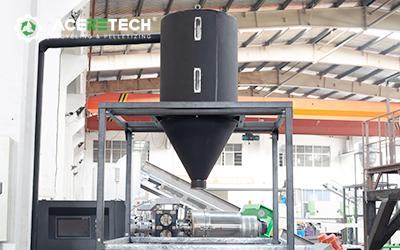
Packing System
- Final qualified granules store here,the drying shaker together with the horizontal centrifuge can get a good drying result, and less energy consumption.
- Capacity online monitoring & Quantitative weighting system.