Input Belt Conveyor
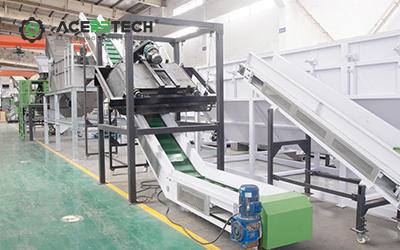
Feeding conveyor to the shredder
Built in heavy duty version;
With load related controlling device for conveyor belt for avoiding of the overfeeding of the shredder;
Metal detector as optional, for detection of metallic contaminants for protecting of the shredder;
Belt conveyor can be PVC/Rubber material;
The speed of belt conveyor is controlled by inverter.
Shredder
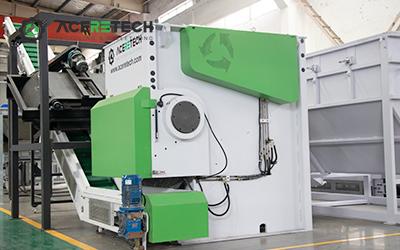
Advantages:
35% more space inside the cutting chamber ;
Built-in hydraulic ram;
Variable faster ram movement;
Less space occupied than traditional shredders
with horizontal rams;
Enclosed cutting chamber to prevent materials flying out.
L Type Belt Conveyor
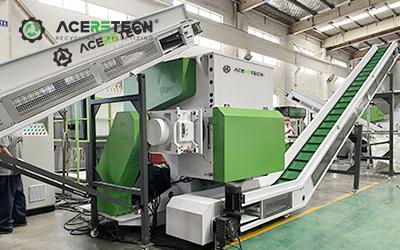
1. For conveying flakes out from shredder.
2. PVC belt.
3. With inverter for speed adjustment.
Magnetic Separation Belt

Magnetic separation belt can be optional item install on the discharge belt conveyor from shredder, it can autocratical removing ferrous metal by permanent magnet.
Pre-Washer
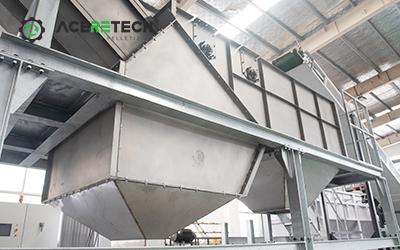
The separation tank, built in stainless steel; Discharge drum; Double discharge system for “heavies”, motorized valves; With pneumatic water in-feed-valve, automatic level control via electronic feeder; With compressor blower to inject compressed air to the bottom of the tank; With working platform; Water and energy saving design.
Crusher
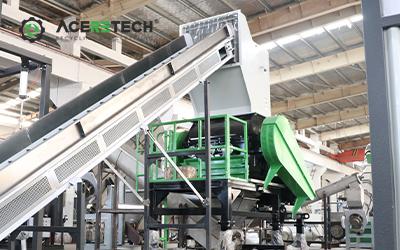
Crushing with water flushing in; 3/5/7 rotor design; Knife adjustment outside chamber; Low noise.
Trommel
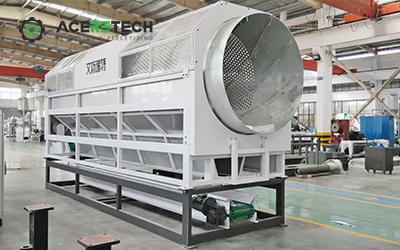
Remove stone, dust, loosen caps and small metal.
5-L type belt conveyor
Feeding conveyor to the next machine:
L Type belt conveyor connected with the Trommel
Equipped with pull switch surround the conveyor.
Screw Loader
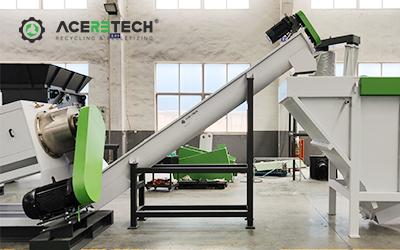
To convey plastic flakes out of crusher into friction washer;
Parts, that contact with water are made of SUS304.
Friction Washer
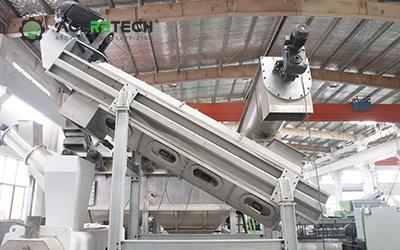
Friction washer as tough washing unit, to removes most of contaminates; Housing built in stainless steel, welded construction; Reinforced, mild steel and high speed rotor; Oversized, outside mounted bearings; Stainless steel screen, hole size 3 mm; Stainless steel feed - and discharge hoppers for the plastic flakes; Water discharge at the bottom.
Floating Washer
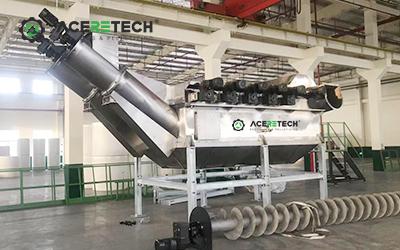
For separation of contaminants or other plastics with gravity > 1 g/cm³ from PE/PP flakes; With screw-IN and screw-OUT; Special design of inner paddles to guarantee sufficient sediment of heavy impurities; Stainless steel SUS304 body; With pneumatic water in-feed-valve, automatic level control via electronic feeler.
Drying System
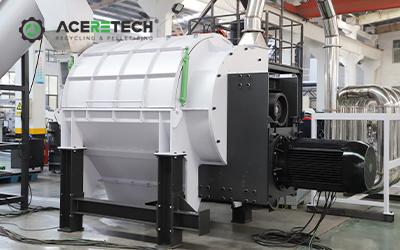
Handling different material, we have different kinds of drying system, squeezer or centrifugal dryer&pipeline dryer, depends on customer requirement. For soft material such as film we can either use squeezer or centrifugal dryer, after drying, material moisture will be controlled wiithin 5-8%, for rigid plastic material, we can use centrifugal dryer and pipeline dryer system, after drying, material moisture will be less than 1%.
Pipe Drying System
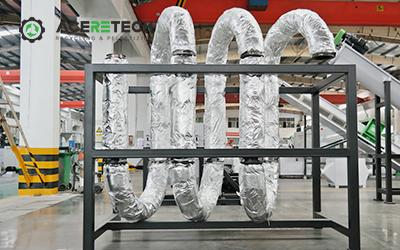
With connecting pipes to the dryer;
Connecting pipes to the cyclone installed above the thermal dryer;
Parts in contact with material built in stainless steel.
Storage Silo
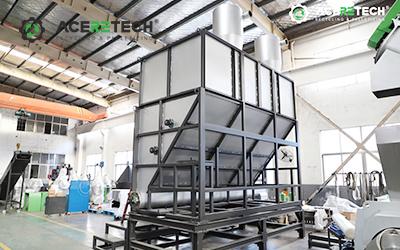
To guarantee non-stop work and stable feeding for downstream extrusion pelletizing line, we will use a buffer silo to storage washed material. Special design can ensure no-blockage for material, at top of the silo, cyclone device for dust removing.
Electrical Cabinet
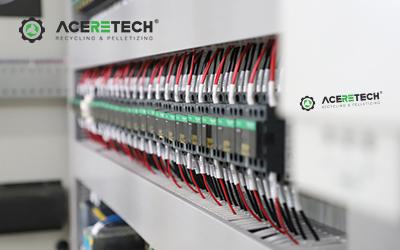
Electric control component: (Schneider), e.g. Circuit-breaker, AC contact, press button, pilot lamp; For electrical controlling of the entire system; Safety interlock principle; All electrical units: LS, Schneider, ABB.
Intelligent Control System
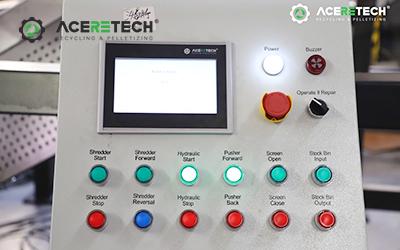
Equipped with an intelligent control system, it can provide appropriate temperature, flow, pressure and concentration to ensure the cleaning effect, better operation interface and monitoring function, making maintenance and troubleshooting easier.