SSP (Continuity) PET Plastic Recycling Machine Line with Solid State Polymerization For IV Increase
SSP (Continuity) Pet Waste Recycled Plastic Pelletizing Machine For IV Increase
Solid state polymerization (SSP) is a post-processing technique used to increase the molecular weight of polyethylene terephthalate (PET), which in turn enhances the melting point, mechanical properties, and chemical stability of PET. This process is commonly employed in the production of bottle preforms and other PET products. The solid state polymerization process takes place attemperatures below the glass transition temperature and above the melting point of PET, allowing the PET particles to remain in a solid state.The advantage of solid state polymerization (SSP) lies in its ability to increase the molecular weightof PET without compromising the material's properties. This is directly related to the performance of the final product, such as improved mechanical strength and enhanced chemical stability.Further more, the SSP process can also remove low molecular weight substances from the material, such as residual monomers and oligomers, thereby increasing the purity of the product. SSP (Solid State Polymerization) is an indispensable step in the manufacturing of PET bottles, containers, packaging tapes, and other engineering plastic products, especially for applications that require high-performance PET.
Recycling & Material
SSP (Continuity) Pet Waste Recycled Plastic Pelletizing Machine For IV Increase
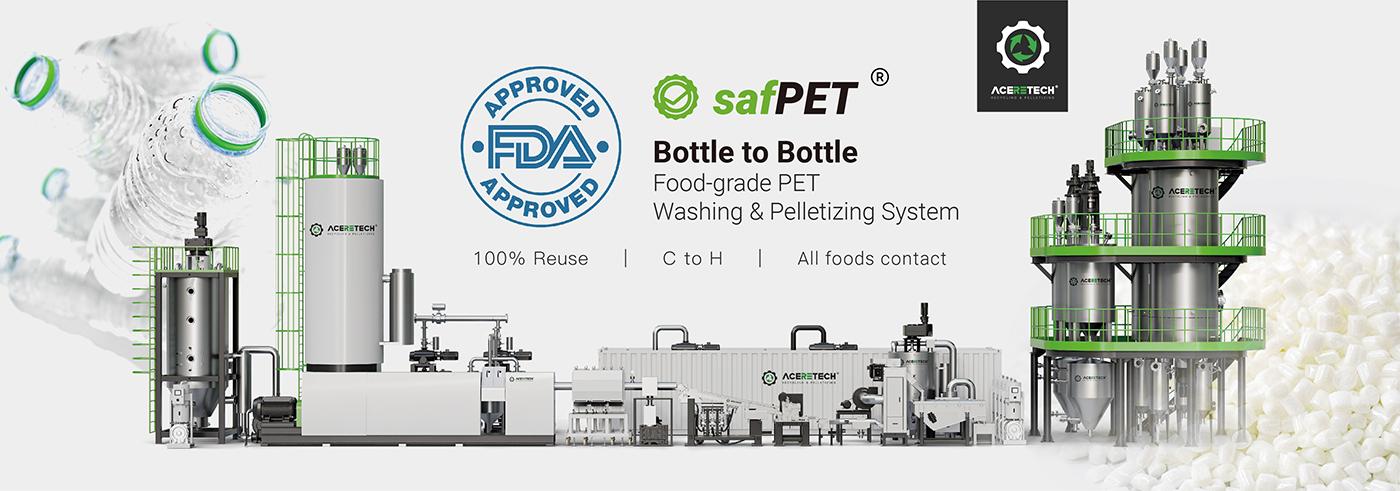
The latest efficient recycling solution. Thanks to the vacuum technology, the SSP IV increasing technology, and the pelletizing extruder specially made by Aceretech, the IV value of the final PET granules can meet the requirements, and this value can be stably maintained. Even there are uneven IV values and moisture content of the raw materials, the final pellets can be maintained at a reasonable, qualified IV value within a set interval, meanwhile the quality and the output are always stable. It can maintain a stable IV value output for further downstream processing and molding, such as stretch blow molding, up to 100% bottle-to-bottle technology in new bottles.
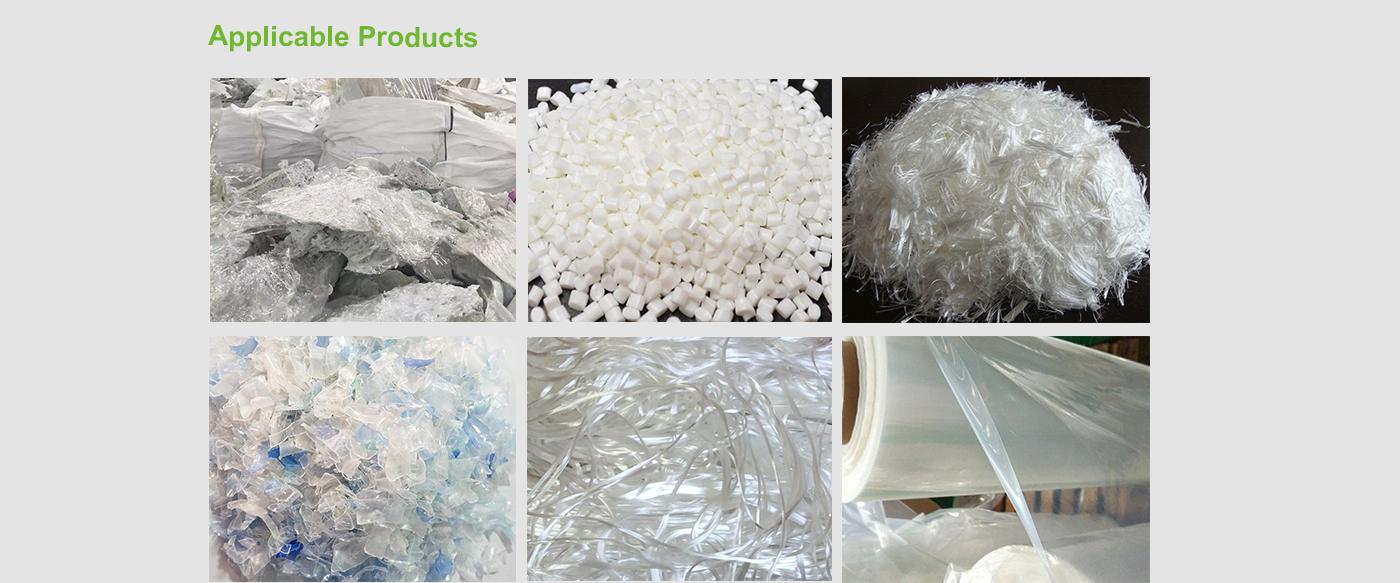
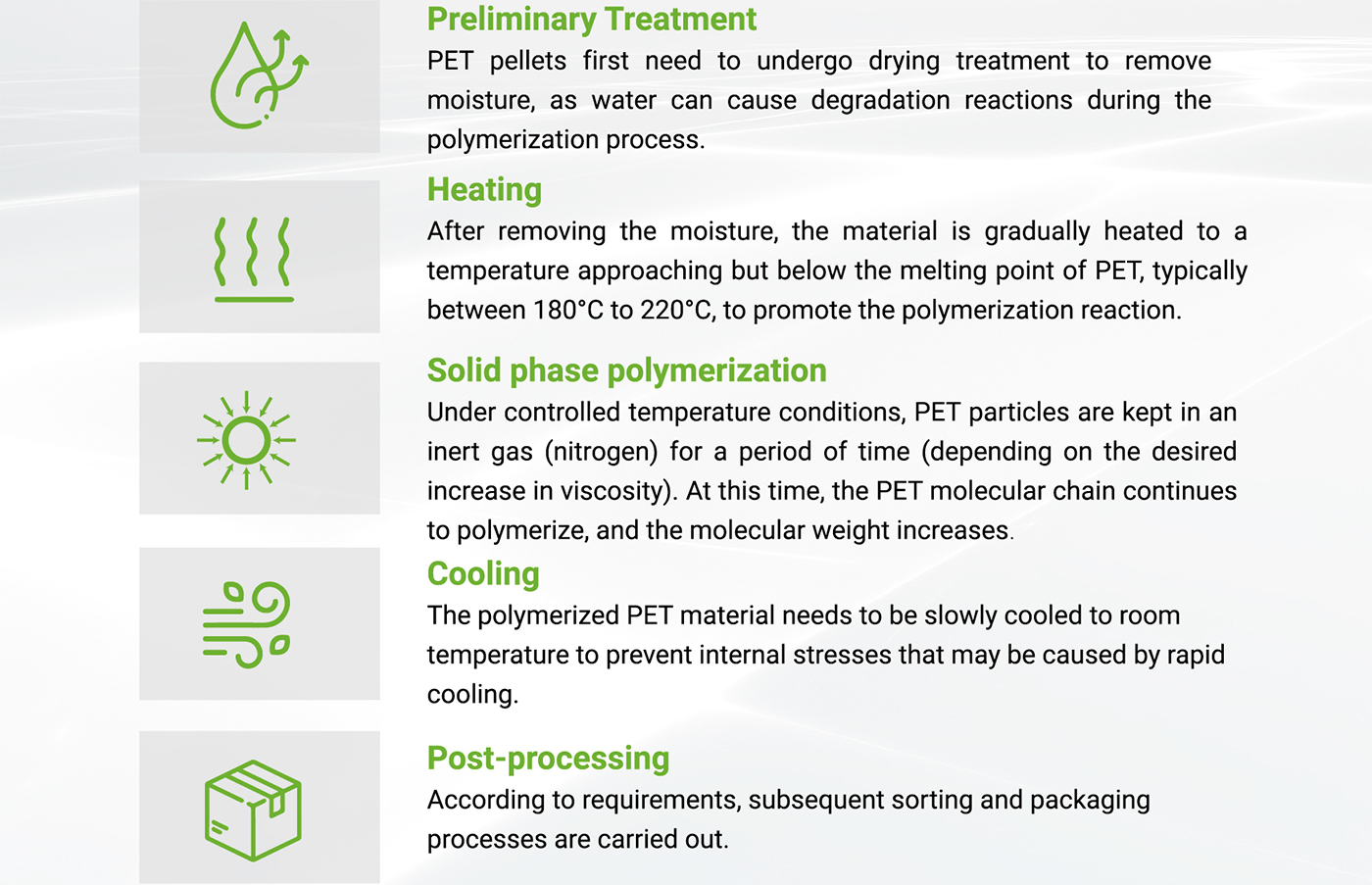
* Higher viscosity increase efficiency, with a maximum actual viscosity increase of 0.02 per hour.
* Two sizes, 12000L and 24000L, modular design, can be freely combined according to production capacity.
* Digital control, user-friendly interface, easy to operate.
* Compared to traditional polymerization processes, the production assembly is modularized andminiaturized, making post-maintenance and operation simple.
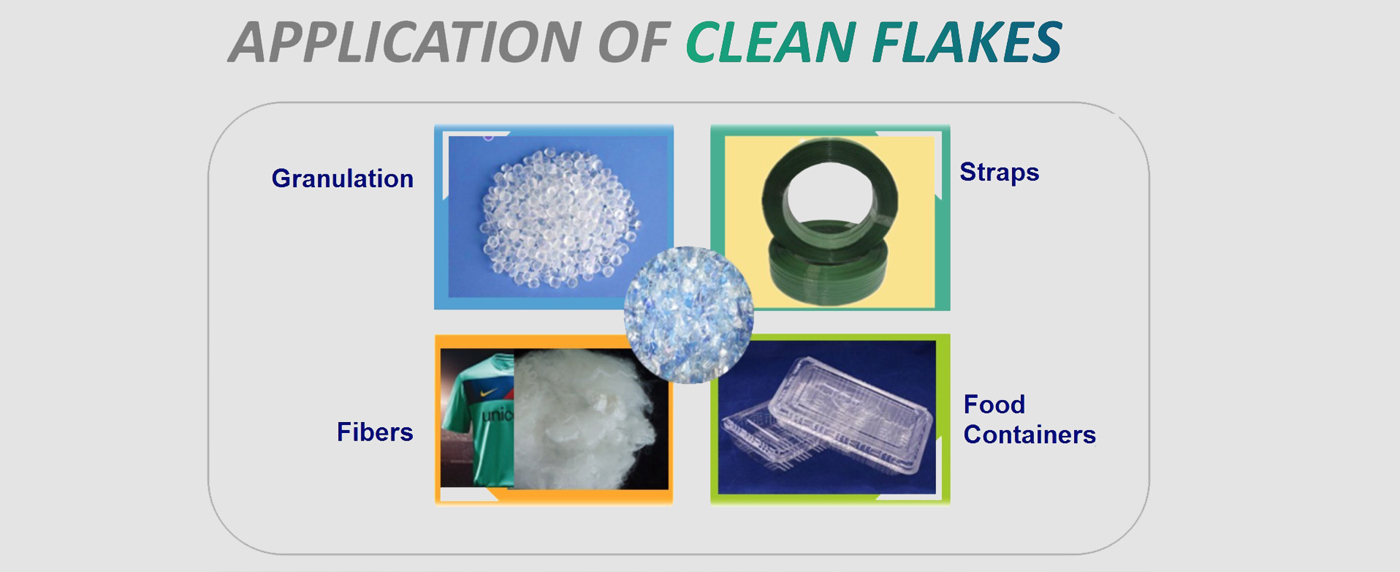